Looking to Start a Business? Get Into 3-D House Printing ASAP
We need to build 1+ billion homes in the next 28 years
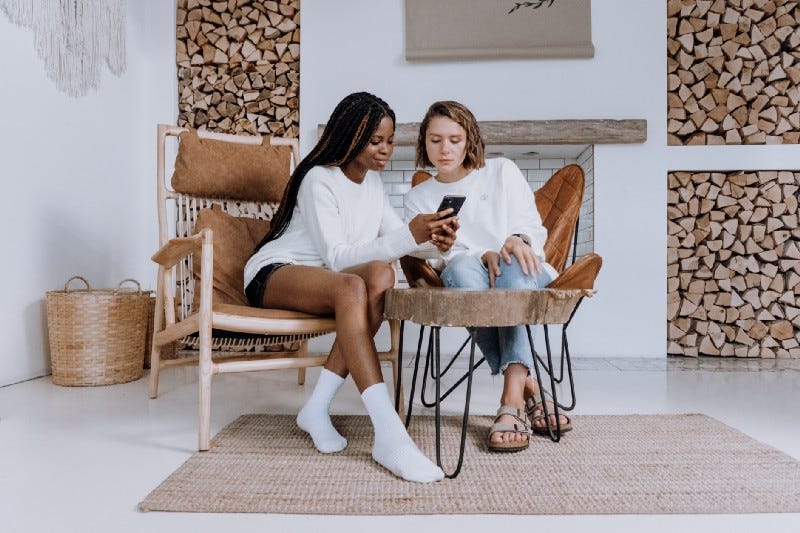
It’s time for Rome to rise again.
No, I’m not talking about the so-called Pax Romana, or their eagle-obsessed war machine, or their endless crucifixions and slavery.
I’m talking about their building materials.
Like the Egyptian pyramids, Roman concrete is the stuff of legends. We still don’t know their exact recipe — all we know is that it’s a geopolymer mix that’s essentially man-made rock that’s somehow getting stronger after all these centuries, even underwater. In fact, the Pantheon in Rome is still the largest unreinforced concrete dome in the world, more than 2,000 years after it was built.
Discoveries in the world of concrete (and rediscoveries of ancient secrets) are the future of housing.
If you’re a young entrepreneur, or a seasoned businessperson looking for a blazing hot new opportunity, seriously consider starting a local 3D-printed house-building company. After all, construction is a $20 trillion annual business and it’s the second-least innovative space behind agriculture.
I recently sat down with Henrik Lund-Nielsen, CEO of COBOD (a manufacturer of 3-D house printers) to discuss technology, competitiveness, environmental impact, market demand, and startup costs.
Let’s dig in.
The technology
In case you’re wondering, COBOD stands for “Construction of Buildings On Demand.” (It’s dumb, I know. These are engineering nerds, after all.)
But don’t worry, their technology is going to change the world.
Their flagship product is the BOD2 — the world’s first “second-generation 3-D construction printer.” It’s a modular machine, meaning it’s easy to set up, move, and maintain.
You basically move it to your next building site, set it up, and it prints a house/office/store for you. It can be <500 square feet or 4000+ square feet, and up to three stories in height, though they’re working on a bigger machine to go even higher.
Currently, about 25–35% of the house construction process can be automated in Europe and America, but COBOD is hoping to double that figure in the near future in order to make housing significantly more affordable. A loss of jobs is, of course, a huge concern at Surviving Tomorrow, but if house prices fell drastically, we’d see significantly more demand which could lead to net job creation.
Demand for COBOD house printers doubled in 2019, doubled again in 2020, and tripled in 2021. (They currently have 75 employees and will likely hit 500+ employees within 5 years.) In fact, they’re so consistently profitable that they don’t even accept investors.
Competitiveness
3-D printed concrete houses cost up to 50% less than regular brick construction.
And now that lumber has doubled in price, concrete is competitive with stick-built houses, too — never mind the fact that concrete can well outlast anything made of wood.
In fact, the estimated lifespan of a concrete house is well over a century.
Environmental impact
Modern concrete gets a bad rap, and deservedly so. Its main ingredient is cement, which is notorious for CO2 emissions due to the huge amounts of heat and energy required to make lime.
That said, concrete’s CO2 emissions per unit of strength are already better than bricks or steel. Plus, CODOD can seriously optimize overall material usage — you don’t even need pouring forms.
The upside with concrete is that you can source 99% of your ingredients locally. Additionally, cement manufacturers are working on relatively “green” cement, and COBOD can also 3-D print with my favorite building material of all time… hempcrete.
Weed-based buildings aside, cement is “the most abundant man-made material on the planet at 8% of global emissions,” but that will all change pretty soon thanks to a Chris Sacca-funded company called Sublime Systems. I’ve chatted with CEO Leah Ellis, whose wonderful wizards have figured out a way to make cement at room temperature using chemical magic and renewable electricity to make carbon-free lime.
Friends: This is how houses will be built in the future.
Market demand
Shelter is the ultimate human need. As the old survivalist adage goes: “You can go three weeks without food, three days without water, but only three hours without heat.”
Which is why you need to know this important statistic:
There are currently one billion people living in slums.
That’s 1,000,000,000 of your brothers and sisters.
That number is growing by more than one million people per day and is expected to hit 3 billion within 28 years.
And that’s just the developing world.
As anti-commons predator monopolies like Airbnb, vampire hedge funds, and grasping multinational banks continue to hoover up the housing market in an attempt to turn the Western working class into rent serfs, there’s also the opportunity to build hundreds of millions of new housing units across North America and Europe.
And we haven’t even mentioned the fact that the global population is conservatively projected to grow by 3.6 billion people by 2100.
All told, we’ll need to build at least two billion new houses in the next 80 years.
So I think there’s a market.
Startup costs
Depending on the size of your unit, a BOD2 machine will cost you anywhere from $300,000 to $600,000.
Including your team, materials, marketing expenses, and your 1–3 weeks of training (it’s that straightforward), you’re looking at an initial outlay of just under $1 million.
That’s less than the cost of a house in Toronto or a condo in New York.
Not bad, considering a BOD2 can print more than one house per week for ten straight years.
In fact, houses of <500 square feet can be printed in a single day. (This one took 12 hours.) Plus, your business basically markets itself — think of all the free publicity you’ll get when you’re the first person to 3D-print a house in [insert country/region/state/county/city/neighborhood.]
In conclusion
As you can see, 3-D printing houses is an exciting and desperately-needed business that will continue to experience massive growth for decades to come.
Plus, 3D-printing high-quality houses gives young entrepreneurs the opportunity to quite literally leave their mark on the planet — like our Roman forebears, maybe someone reading this article will build a building that’s still enjoyed two millennia from today.
If you and/or a group of friends and colleagues can find financing, I’d seriously encourage you to get into 3-D printing houses.
This is a real, productive, contributive business — a growing rarity in our age of money-losing wealth-destroying zombie companies.
Not only will you meet a real human need, spread social justice, and help create wider-spread wellbeing and human flourishing, but you’ll be part of contributing something of value that is quickly disappearing in our commodify-everything age:
Home.
If you think this article is important, please forward it to a friend and share it on social media.